Historia oświetlenia - produkcja ostatniej lampy MH w Polsce
: piątek 21 mar 2014, 15:32
Przedstawiam dokument, który pokazał się już dwa lata temu na forum lighting-gallery.pl, ale ze względu na sprawy związanie z samą pracownią, był wyłącznie w dziale dla zarejestrowanych użytkowników. Sprawa dotyczy Pracowni Lamp Wyładowczych Instytutu Elektrotechniki. Strona jeszcze istnieje, mimo to, że pracowni dawno nie ma.
Przedstawiam Wam proces produkcji ostatniej metalohalogenkowej lampy wyładowczej wyprodukowanej od zera w Polsce. Ostatnia sztuka w jedynej takiej pracowni w kraju i jednej z zaledwie kilku w Europie.
Prześledzimy go od początku do końca. Zdjęcia wrzucam jako miniaturki, gdyż jest ich sporo.
Najważniejszym elementem lampy wysokoprężnej jest jarznik, w tym przypadku jest on kwarcowy, powstaje w wyniku stopienia trzech rurek i wtopienia dodatkowej rurki pompowej.
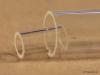


Zapas rurek pompowych
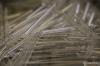
Rurki te są stapiane w płomieniu.
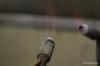
Powstały w tym procesie element kwarcowy jest umieszczany w maszynie do obsadzania elektrod. Elektrody są przygotowane wcześniej, wygrzewane, czyszczone, kiedyś nakładało się pastę emisyjną, obecnie kupuje się gotowy półprodukt.
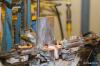
Od dołu wkłada się elektrody z emiterem, od góry korek z rurką, przez którą przepuszcza się gaz obojętny.
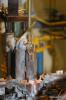
Pracownik opuszcza jarznik w dół urządzenia, gdzie jest on mocno nagrzany precyzyjnymi palnikami, a następnie zaciśnięty, tworząc spłaszcz.
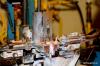
Szkło kwarcowe bardzo się przy tym nagrzewa, dlatego trzeba patrzeć przez szybkę.

Urządzenie do tworzenia spłaszczy w jarzniku jest półautomatem, wymaga jednak niesamowitej wprawy - tego nie zrobi ktoś, kto nie ma doświadczenia. Napęd jest sprężonym powietrzem, oprócz tego niezbędny jest przepływ gazów technicznych, by nie zniszczyć jarznika parą wodną.

A tak wygląda całość urządzenia.

Zatopiony jarznik wygląda tak:
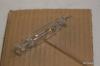
Albo tak.
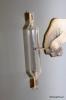
Po odpompowaniu ma on próżnię, którą sprawdza się generatorem wysokiego napięcia - to ma świecić
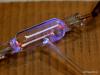
Potem jarznik napełnia się na takim stanowisku gazem o odpowiedniej jakości (argon spektralny).
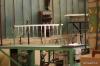
Elementy się przygrzewa, uzupełnia atmosferę i zatapia, w przypadku lamp rtęciowych dozując rtęć w postaci amalgamatu.

Jeśli jest to lampa rtęciowa, to najważniejszy proces jest już zakończony, jeśli jest to lampa halogenkowa, to precyzyjnie odmierzone ilości halogenków metali muszą być zadozowane w komorze laminarnej, w której panuje kontrolowana atmosfera (brak wilgoci, para wodna w ilościach mierzonych w ułamkach części na milion)
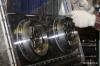
Rurka pompowa jest podawana do komory przez śluzę gazową. Pracownik od góry wsypuje do rurki odmierzoną ilość grudek zawierających gotowe substancje. Dawniej odważano porcje ręcznie, dlatego lampy LRJD i LRJ były tak kapryśne - trudno było ustalić precyzyjnie ilość składników. Później kupowano gotowe mikropastylki (średnica poniżej 1mm).

Po zadozowaniu halogenków i uzupełnieniu gazów argonem spektralnym i odmierzoną ilością amalgamatu rtęci, rurka pompowa jest zatopiona.
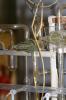
Jarznik jest gotowy. Jeśli jest to lampa bez zewnętrznej bańki, to wystarczy przylutowanie przewodów i wklejenie trzonka na kit.
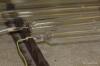
Jeśli jest to lampa z zewnętrznym balonem, to trzeba jeszcze przygotować ramkę i przeprowadzić proces zatapiania i odpompowania balonu.
Jarznik jest mocowany do ramki, która powstanie z oczyszczonych materiałów. Niektóre z nich czyści się na elektrolizerze
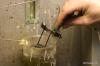
A następnie przemywa w różnych rozpuszczalnikach i zgrzewa ze sobą na zgrzewarce punktowej, mocując do szklanego spłaszcza (traktujemy go jako prefabrykat, powstał na nóżkarce w osobnym procesie technologicznym).
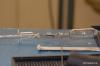


Widoczny drut jest wykonany z molibdenu.

W tym czasie zatapiarka jest już rozgrzana

Do zatapiarki wkłada się balon z ramką w środku i centruje
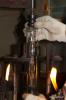
Balon jest przytrzymywany zaciskami śrubowymi
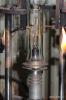
i przytrzymywany u góry przez talerzyk

Palniki ogrzewają szkło, ramka trzymająca balon lampy się obraca.




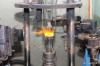
Po nagrzaniu, nadmiar szkła jest odcinany, podciśnienie zgina szkło, a później nagrzane szkło jest formowane w kształt gwintu przez zaciskane szczęki.

Wychładzanie lampy
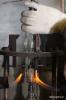
spłaszcz jest zatopiony

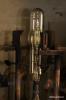
Tak wygląda balon po zatopieniu na zatapiarce

Ramka trzyma się u góry balonu za pomocą odpowiednio wygiętych drutów
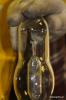
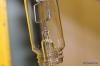
Teraz pora na odpompowanie bańki zewnętrznej na specjalnym stanowisku pompowym

Zadozowanie gazów technicznych (argon)

Wkręcenie trzonka, do którego lutowane będą przewody ze spłaszcza bańki. Po wlutowaniu, lut spływa do środka trzonka metalowego, zabezpieczając lampę przed wykręceniem się z trzonka.

Jeśli w bańce jest getter, trzeba go rozpylić, robi się to wygrzewając lampkę za pomocą pieca indukcyjnego (3kW, 400kHz)
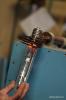
Pora na próby:
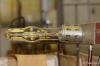
start!



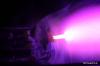
Ostatnia operacja - pakowanie.

Zapakowałem ostatnią lampę wyprodukowaną w ostatnim nieprzemysłowym laboratorium lamp wyładowczych w Polsce. Pół godziny później zatapiarka została trwale odłączona, dwa tygodnie później pracownia już nie istniała.
Obejrzeliście coś, czego nikt dotąd z taką dokładnością nie udokumentował na publicznym forum.
Obecni producenci w kraju nie wytwarzają już w ogóle najważniejszego elementu lampy MH, jakim jest jarznik. Obecnie importuje się jarzniki, głównie z Chin. Nikt nie ma już w kraju technologii, która umożliwiłaby budowę lampy od zera, od szkła, metalu i chemii.
Przedstawiam Wam proces produkcji ostatniej metalohalogenkowej lampy wyładowczej wyprodukowanej od zera w Polsce. Ostatnia sztuka w jedynej takiej pracowni w kraju i jednej z zaledwie kilku w Europie.
Prześledzimy go od początku do końca. Zdjęcia wrzucam jako miniaturki, gdyż jest ich sporo.
Najważniejszym elementem lampy wysokoprężnej jest jarznik, w tym przypadku jest on kwarcowy, powstaje w wyniku stopienia trzech rurek i wtopienia dodatkowej rurki pompowej.
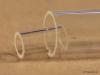


Zapas rurek pompowych
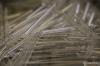
Rurki te są stapiane w płomieniu.
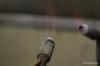
Powstały w tym procesie element kwarcowy jest umieszczany w maszynie do obsadzania elektrod. Elektrody są przygotowane wcześniej, wygrzewane, czyszczone, kiedyś nakładało się pastę emisyjną, obecnie kupuje się gotowy półprodukt.
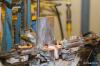
Od dołu wkłada się elektrody z emiterem, od góry korek z rurką, przez którą przepuszcza się gaz obojętny.
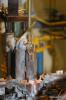
Pracownik opuszcza jarznik w dół urządzenia, gdzie jest on mocno nagrzany precyzyjnymi palnikami, a następnie zaciśnięty, tworząc spłaszcz.
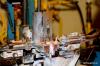
Szkło kwarcowe bardzo się przy tym nagrzewa, dlatego trzeba patrzeć przez szybkę.

Urządzenie do tworzenia spłaszczy w jarzniku jest półautomatem, wymaga jednak niesamowitej wprawy - tego nie zrobi ktoś, kto nie ma doświadczenia. Napęd jest sprężonym powietrzem, oprócz tego niezbędny jest przepływ gazów technicznych, by nie zniszczyć jarznika parą wodną.

A tak wygląda całość urządzenia.

Zatopiony jarznik wygląda tak:
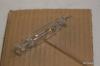
Albo tak.
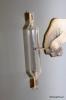
Po odpompowaniu ma on próżnię, którą sprawdza się generatorem wysokiego napięcia - to ma świecić
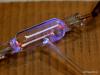
Potem jarznik napełnia się na takim stanowisku gazem o odpowiedniej jakości (argon spektralny).
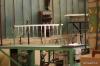
Elementy się przygrzewa, uzupełnia atmosferę i zatapia, w przypadku lamp rtęciowych dozując rtęć w postaci amalgamatu.

Jeśli jest to lampa rtęciowa, to najważniejszy proces jest już zakończony, jeśli jest to lampa halogenkowa, to precyzyjnie odmierzone ilości halogenków metali muszą być zadozowane w komorze laminarnej, w której panuje kontrolowana atmosfera (brak wilgoci, para wodna w ilościach mierzonych w ułamkach części na milion)
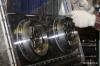
Rurka pompowa jest podawana do komory przez śluzę gazową. Pracownik od góry wsypuje do rurki odmierzoną ilość grudek zawierających gotowe substancje. Dawniej odważano porcje ręcznie, dlatego lampy LRJD i LRJ były tak kapryśne - trudno było ustalić precyzyjnie ilość składników. Później kupowano gotowe mikropastylki (średnica poniżej 1mm).

Po zadozowaniu halogenków i uzupełnieniu gazów argonem spektralnym i odmierzoną ilością amalgamatu rtęci, rurka pompowa jest zatopiona.
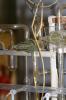
Jarznik jest gotowy. Jeśli jest to lampa bez zewnętrznej bańki, to wystarczy przylutowanie przewodów i wklejenie trzonka na kit.
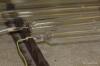
Jeśli jest to lampa z zewnętrznym balonem, to trzeba jeszcze przygotować ramkę i przeprowadzić proces zatapiania i odpompowania balonu.
Jarznik jest mocowany do ramki, która powstanie z oczyszczonych materiałów. Niektóre z nich czyści się na elektrolizerze
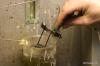
A następnie przemywa w różnych rozpuszczalnikach i zgrzewa ze sobą na zgrzewarce punktowej, mocując do szklanego spłaszcza (traktujemy go jako prefabrykat, powstał na nóżkarce w osobnym procesie technologicznym).
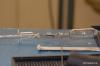


Widoczny drut jest wykonany z molibdenu.

W tym czasie zatapiarka jest już rozgrzana

Do zatapiarki wkłada się balon z ramką w środku i centruje
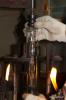
Balon jest przytrzymywany zaciskami śrubowymi
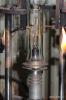
i przytrzymywany u góry przez talerzyk

Palniki ogrzewają szkło, ramka trzymająca balon lampy się obraca.




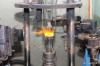
Po nagrzaniu, nadmiar szkła jest odcinany, podciśnienie zgina szkło, a później nagrzane szkło jest formowane w kształt gwintu przez zaciskane szczęki.

Wychładzanie lampy
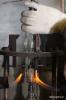
spłaszcz jest zatopiony

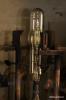
Tak wygląda balon po zatopieniu na zatapiarce

Ramka trzyma się u góry balonu za pomocą odpowiednio wygiętych drutów
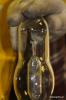
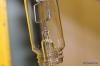
Teraz pora na odpompowanie bańki zewnętrznej na specjalnym stanowisku pompowym

Zadozowanie gazów technicznych (argon)

Wkręcenie trzonka, do którego lutowane będą przewody ze spłaszcza bańki. Po wlutowaniu, lut spływa do środka trzonka metalowego, zabezpieczając lampę przed wykręceniem się z trzonka.

Jeśli w bańce jest getter, trzeba go rozpylić, robi się to wygrzewając lampkę za pomocą pieca indukcyjnego (3kW, 400kHz)
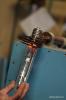
Pora na próby:
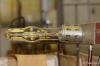
start!



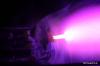
Ostatnia operacja - pakowanie.

Zapakowałem ostatnią lampę wyprodukowaną w ostatnim nieprzemysłowym laboratorium lamp wyładowczych w Polsce. Pół godziny później zatapiarka została trwale odłączona, dwa tygodnie później pracownia już nie istniała.
Obejrzeliście coś, czego nikt dotąd z taką dokładnością nie udokumentował na publicznym forum.
Obecni producenci w kraju nie wytwarzają już w ogóle najważniejszego elementu lampy MH, jakim jest jarznik. Obecnie importuje się jarzniki, głównie z Chin. Nikt nie ma już w kraju technologii, która umożliwiłaby budowę lampy od zera, od szkła, metalu i chemii.